Initial Build
Introduction
What if you could take your micromobility solution anywhere with you? On a bus, a train, or even a commercial airplane? That’s the goal of this build: a fast scooter that weighs under 50 lbs, with 10 inch wheels, can go over 30 mph, and fit in an overhead bin on an airplane without sacrificing the stability and confidence of larger ‘superscooters.’ That’s what I’m working on. Basically, an electric moped that fits anywhere. Curious? Here’s a blog about what I’ve done so far. First, check out the cool renders of some of the design concepts. Then, check out the build progress.
Initial Inspiration:
As a former competitive motorcycle racer and frequent traveler, I’ve always been inspired by oddball bikes like the Bimota Tesi. Though suspension has gotten really good, few manufacturers have experimented much with alternative front-ends, other than BMW with tele-lever/duolever, and Bimota with the Tesi. Initially, I wanted to build a hyperscooter with sportbike performance, with features like tunable anti-dive suspension and high quality adjustable motorcycle shocks from Ohlins, Showa, or WP. However, I soon realized that in situations where that sort of performance would be useful, I was always just riding my real motorcycle, a Kawasaki ZX6r. If you want to go 60+ mph, you probably will end up going 100+ before not too long. And the idea of doing 100 mph on 10 inch tires seemed ludicrous at best, and lethally dangerous at worst. So I rethought the design objectives, and came to this new idea: a fast-enough scooter for shorter trips on surface roads that can extend existing transit infrastructure, like trains, subways, buses, or even my friend’s cars when I don’t feel like riding home.
By using a hub centric steering system (HCS), similar to bimota, I thought we could achieve super-scooter levels of stability in a portable scooter sized system. This is because unlike a typical headset based scooter design, a HCS allows the geometry of the steerer tube to be independent of the steerer hub. This is critical on a scooter, because small wheels require bigger rake angles to maintain stability, but on a typical scooter, that bigger rake angle make the effective deck shorter. So it’s a tradeoff between stability and usability. Big scooters like the wolf king gtr get around this lack of rake by adding a steering damper, but passive stability is almost always better than actively damped stability.
The first design:
The original version of the scooter was designed to fold sideways and fit into a carry-on sized bounding box. This required a center folding mechanism, and also for the stem to folder in multiple places and be lower in height than the wheels. I spent a couple months with a contractor designing and building the first version of the scooter. Here are some pictures:
In this version, almost everything was custom other than the rear hub motor and tire, the front brake caliper, and the front tire. Building this scooter took months, and cost a lot more money than would’ve been ideal, especially considering that very few things from this version are still being used.
The main problem with this design was that the front end was too weak. When the scooter was ridden, the front wheel, with its single sided swingarm, would noticeably deflect. And the aluminum swingarms actually bent under the load. This result was expected after confirming the design with FEA, which should’ve been done before the parts were ordered. But I wanted to move forward with the design, rather than sitting on it. And we learned a lot with this initial version!
In initial tests, we literally ziptied an RC plane battery to the inside of the scooter and took it for a spin. I even had to 3d print an adapter for the throttle, since i bought the wrong one.
Here’s a video of it being ridden.
Despite the issues with the front end, it’s still one of the most stable scooters i’ve ridden, so we were able to verify that the front end geometry really did make a difference!
V1.1
The next step was to figure out a way to add the front brake, and reinforce the front end so it wouldn’t deflect under the weight of the rider. In this case, we learned our lesson and did FEA on the design before building it.
We also designed it to be simply made out of welded square tubes, with 3d printed jigs to hold everything together. The jigs are essentially single use items, unless you’re very careful with tac welding, and I wouldn’t recommend building your scooter with flux core welder and no welding table, but that was what we had, and we wanted to get it done. See the welding setup pictured here:
It bolted up to the old wheel and hub perfectly.
We also took this opportunity to test out different stem designs, as we felt the original stem was very overbuilt. We tried this stem off of a Xiaomi scooter, which turned out to be too weak. Additionally, the stem bearings were swapped out for bushings, which caused a host of other problems. The stem experiences very high loads, especially under braking, and the bushings caused the stem to bind up in these conditions. Not good!
This was also the first version with a deck, and an extendable stem such that it could be folded down more easily.
We experimented with another aspect of the portability, which was the idea of it folding in half, such that it could be wheeled up and down stairs easily. Seen here, it sort of worked! But not as well as we would’ve hoped.
’
V1.2
Following those modifications, we made some new adjustments. This time, adding a rear footrest, upsizing to a bigger stem diameter, and building a custom telescoping stem from aluminum, rather than using the Xiaomi stem.
We also got the front brake working, which resulted in even more binding caused by the bushings used in the stem. This scooter was the closest we had gotten so far to something reliable and usable!
I even swapped out the wood with a fancy carbon deck, which got rid of the footrest.
V1.3
For the next version, we wanted to simplify the hub, stem, and swingarm setup, and switch back from bushings to bearings for all front-end components to avoid binding. We used the same welded steel + 3d printed jig construction, this time with even less care. The main point of this version was to make sure that the scooter performed as expected with bearings.
We also beefed up the stem, as that had been a big problem before. To do it, we increased the lower stem size to 40mm, and used go kart axle parts to construct it.
The new stem is incredible strong, but it’s also very heavy, as it’s a 1m long 40mm tube with 3mm walls. I had planned to cut it down and add a folding mechanism, but decided that the axle just looked too nice to butcher it up.
The new front-end setup feels about as solid as a Bird or Lime scooter, and it rides with more stability.
A new steering arm was welded up, and after some small adjustments the new scooter was ready to go.
The updated bearing + kart axle front end was the best performing scooter so far, with tons of stability and smooth steering under all conditions.
I’m excited about all the progress we’ve made so far, and looking forward to what’s to come!
V2
The goal of V2 is to incorporate everything we’ve learned so far into an awesome new, limited production run scooter. We’d love your feedback, so if you have any ideas, or are interested in being a beta tester/buyer shoot us an email at scooters@superfastscooter.com, and join the mailing list for future updates!
Here are some cool renders of ideas for the V2.
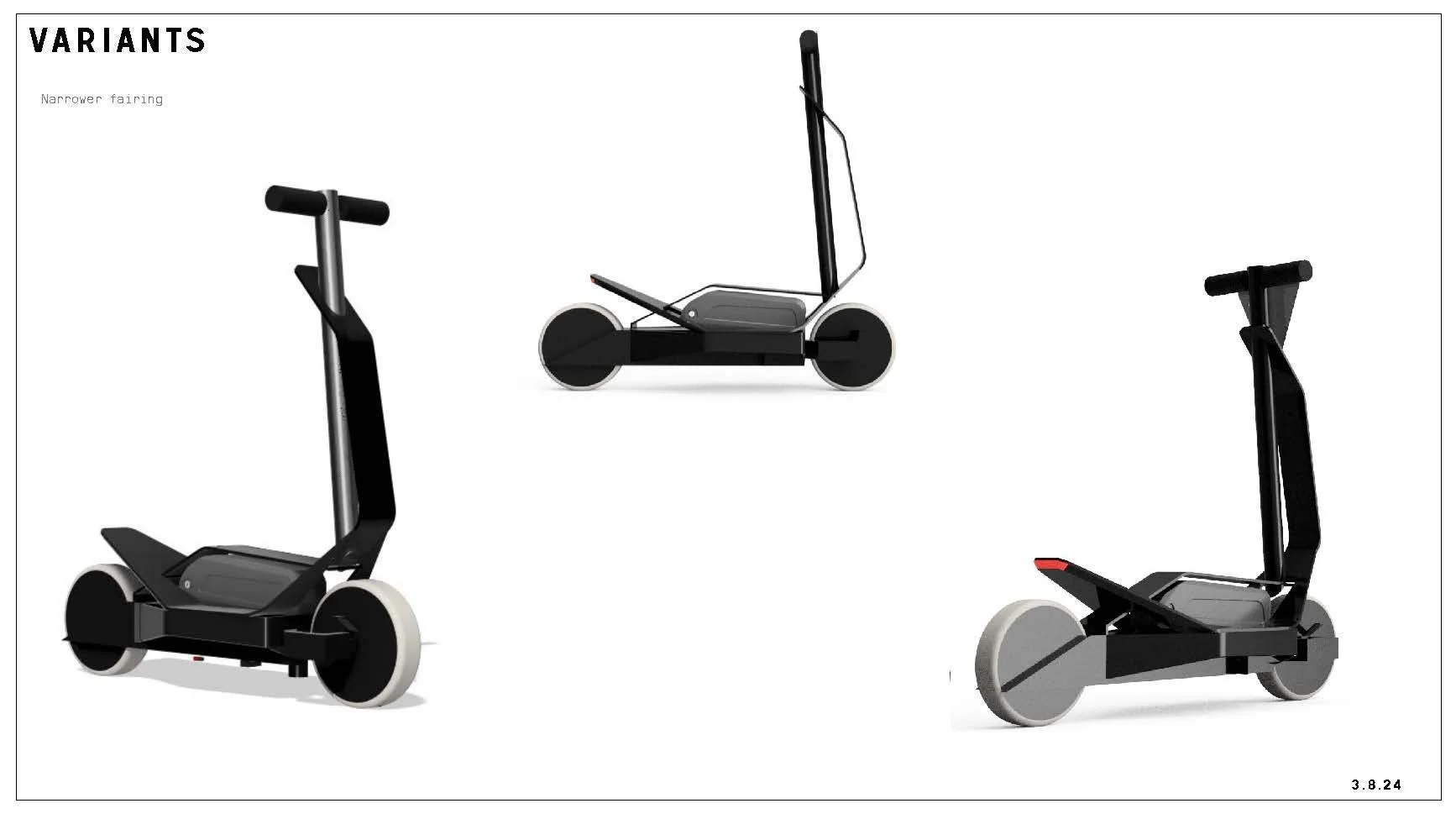

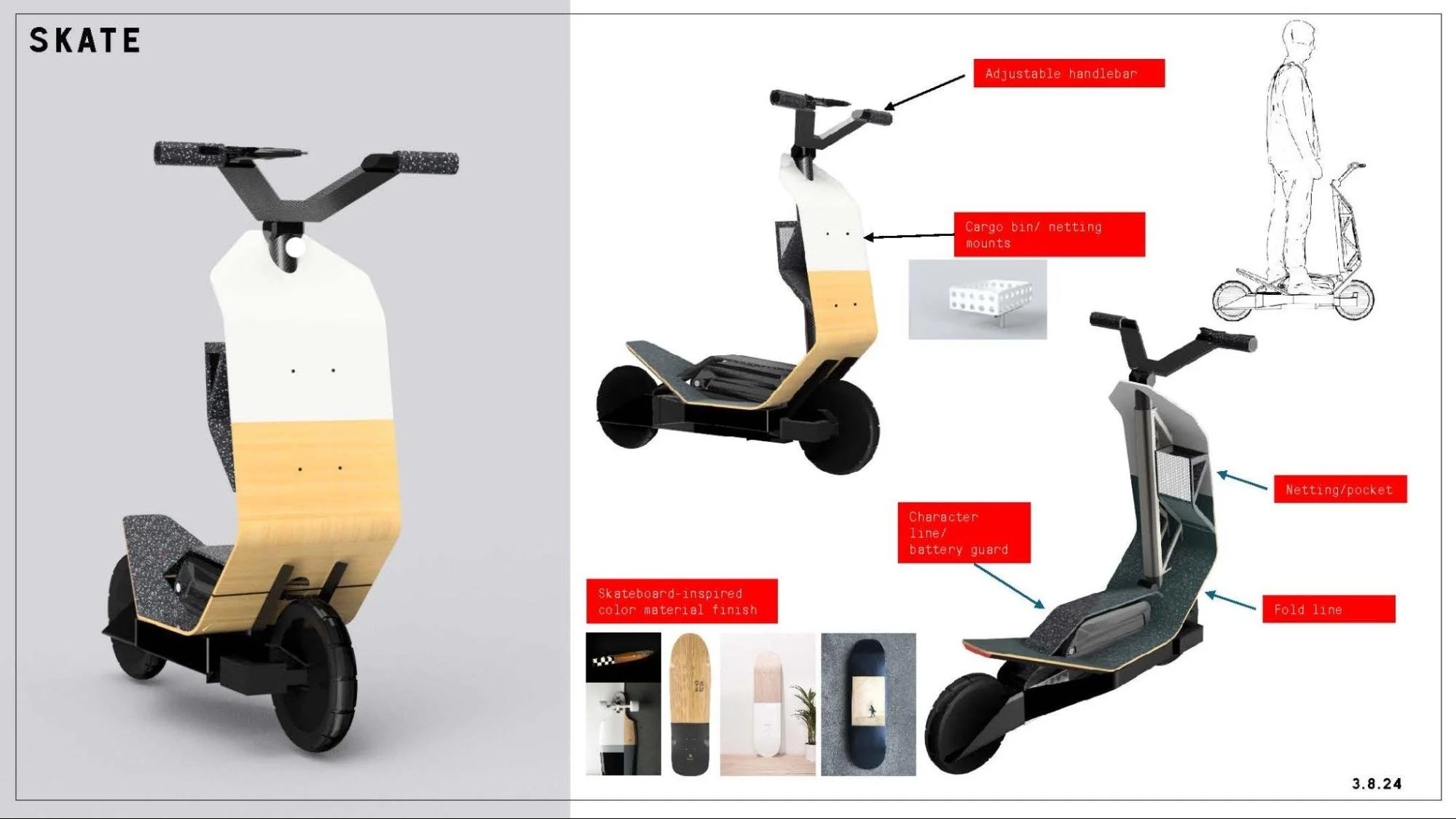
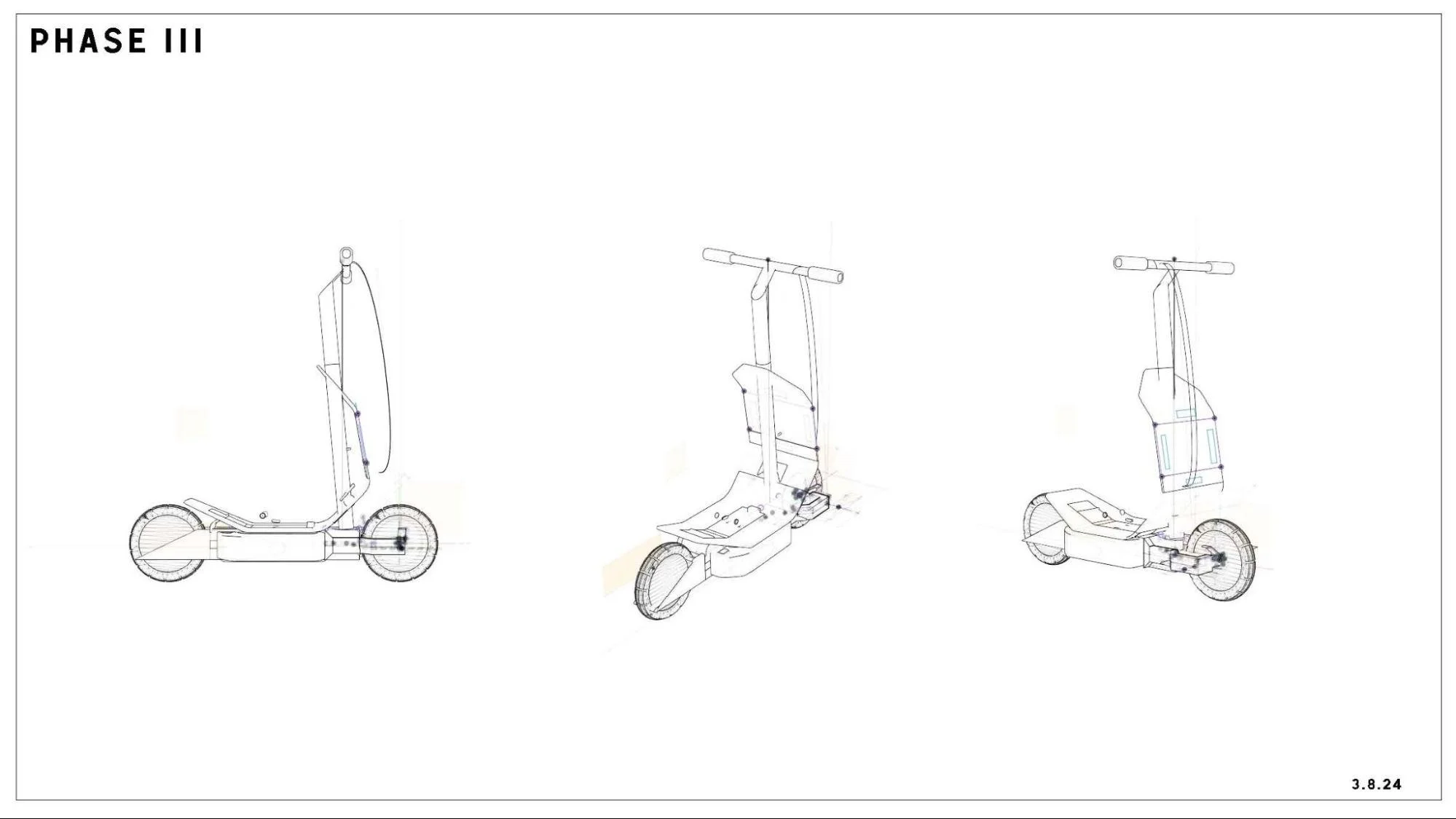